Code Compliant Wall Detailing
This page illustrates the integration of code-compliance requirements and best practices for moisture control of frame wall assemblies (based on 2021 IRC / 2024 IRC). A printable PDF of this information is also available in our Quick Guide library.
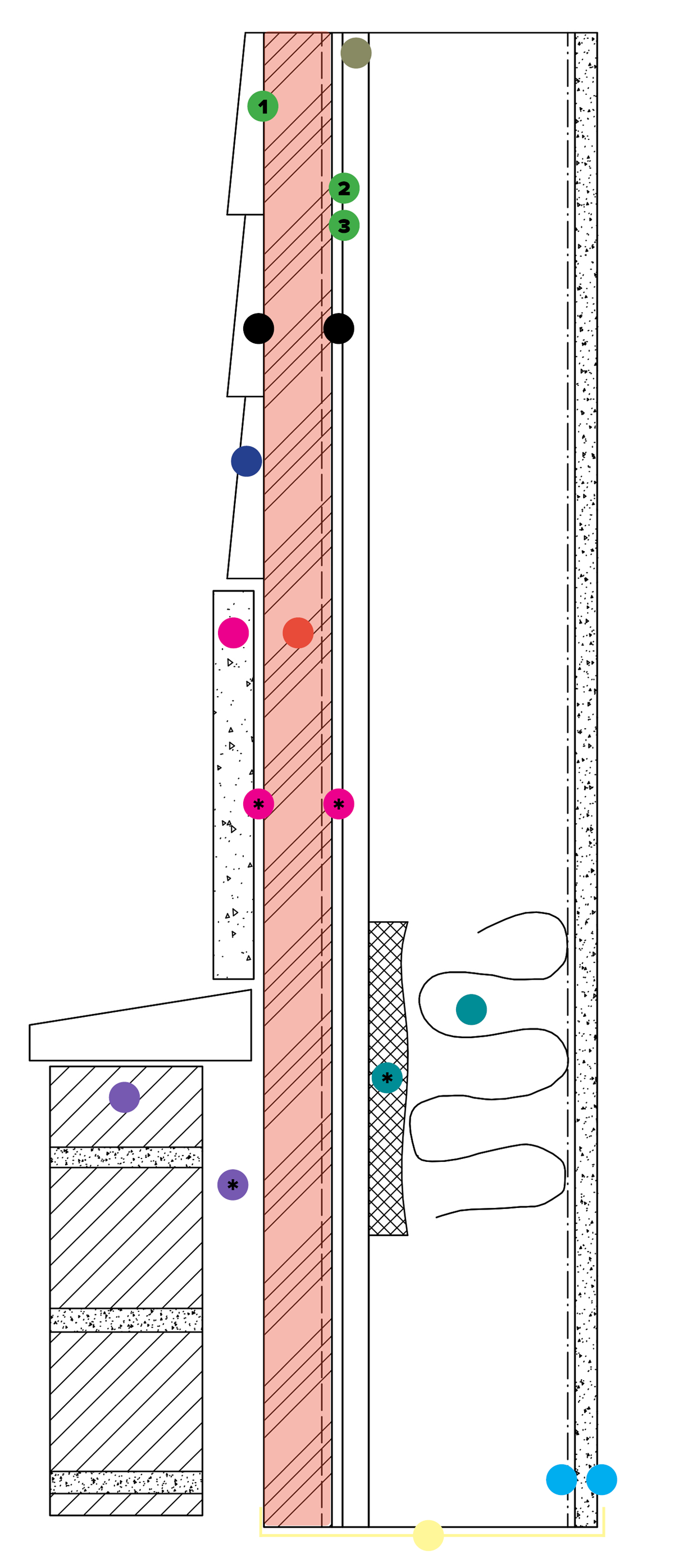
NOTE: Drainable EIFS cladding (not shown) is similar to stucco and drainage between ci substrate and WRB is always required per Section R703.9 (barrier EIFS is not permitted in IRC).
Flashing (IRC Section R703.4): Flashing at siding transitions, fenestration, and other wall penetrations or details not shown; flash to the designated WRB layer (location in wall may vary) and kick-out to exterior or cladding where required at weeps, etc.
Cladding Connections (IRC Section R703.3): For connections through FPIS refer also to IRC Section R703.15.
FIGURE KEY:
ci = continuous insulation
VR = vapor retarder
AB = air barrier
WRB = water-resistive barrier
FPIS = foam plastic insulating sheathing
EIFS = exterior insulation & finish system
ccSPF = closed-cell spray foam
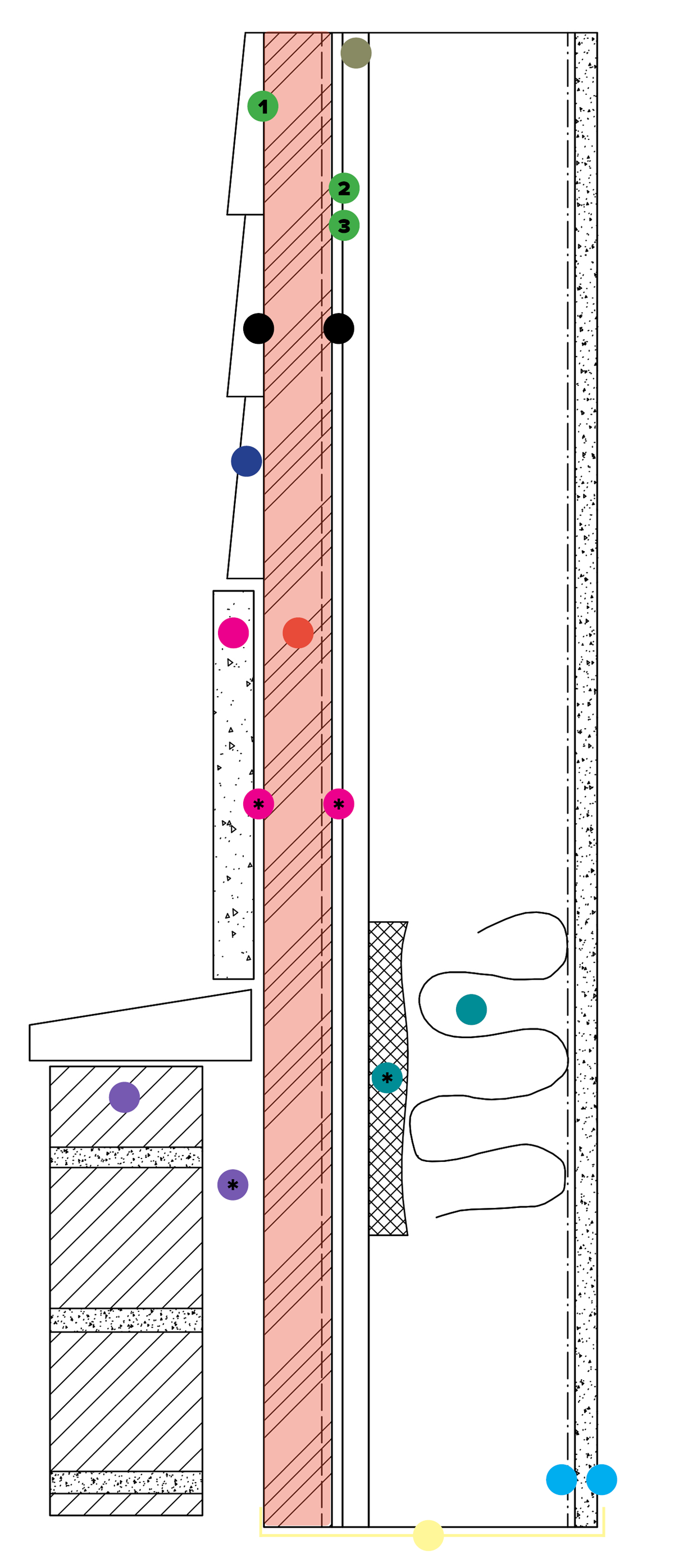

Structural Sheathing
Specify and install structural sheathing per IRC Chapter 6 where used for wall bracing. Examples include OSB, plywood, gypsum sheathing, fiberboard, diagonal wood boards, etc. (Wood let-in and metal brace options not shown.)
Specify and install structural sheathing per IRC Chapter 6 where used for wall bracing. Examples include OSB, plywood, gypsum sheathing, fiberboard, diagonal wood boards, etc. (Wood let-in and metal brace options not shown.)

Water-Resistive Barrier (WRB)
Specify and install a WRB in accordance with IRC Section R703.2. WRB material and location options include:
Specify and install a WRB in accordance with IRC Section R703.2. WRB material and location options include:
- Surface of FPIS WRB System w/ taped joints - FPIS surface used as WRB
- Separate WRB behing ci - Any ci insulation type not used as WRB
- Membrane (wrap), spray-applied, or WRB wall sheathing

Drainage Space (location based on WRB option used)
Where required, located between cladding and WRB (see above). See requirements for reservoir cladding types (brick, stucco, adhered veneer, etc.).* Where not required, use as recommended best practice.
Where required, located between cladding and WRB (see above). See requirements for reservoir cladding types (brick, stucco, adhered veneer, etc.).* Where not required, use as recommended best practice.

Lap Sidings (vinyl, wood, aluminum, fiber-cement, etc.)
Specify and install lap sidings per IRC Section R703. In Climate Zones 4-8 where using a Class III interior VR, two options to control water vapor are provided in Table R702.7(3):
Specify and install lap sidings per IRC Section R703. In Climate Zones 4-8 where using a Class III interior VR, two options to control water vapor are provided in Table R702.7(3):
- Without exterior ci – siding must be back-vented (e.g., furred) or vented siding (e.g., vinyl).
- With exterior ci – siding not required to be back-vented or vented siding.

Stucco, Adhered Masonry Veneer, Cement Panel Siding, etc.
Specify and install WRB per IRC Section R703.7.3. In Moist/Marine climate regions, a minimum 3/16" drainage space is required. See drainage space location options based on WRB location specified.*
Alternative drainage methods include drainage matt, drain wrap, or channeled back of FPIS with separate WRB on its interior side. All alternatives must have minimum 90% drainage efficiency per ASTM E2273 or E2925.
Specify and install WRB per IRC Section R703.7.3. In Moist/Marine climate regions, a minimum 3/16" drainage space is required. See drainage space location options based on WRB location specified.*
Alternative drainage methods include drainage matt, drain wrap, or channeled back of FPIS with separate WRB on its interior side. All alternatives must have minimum 90% drainage efficiency per ASTM E2273 or E2925.

Continuous Insulation (ci)
Where used or required for energy code compliance, ci R-value must meet IRC Table R702.7(2) and Table R702.7(3), (4), or (5) as applicable based on Climate Zone and the interior VR Class specified. The required minimum ci R-values ensure adequate temperature control to prevent condensation and moisture accumulation within the wall. Increasing ci R-values above code-minimums will further improve thermal performance and moisture control.
Where non-vapor permeable (< 5 perm) ci is used (e.g., FPIS), it will mitigate inward vapor drive from reservoir claddings (e.g., stucco, adhered veneer, brick, etc.). For similar reasons, it is recommended to use a moderate to low perm WRB (e.g., < 20 perm) behind a vapor permeable ci material.
NOTE: Combination of ci and cavity R-value must satisfy energy code, where used or required. They cannot be summed to meet energy code.
Where used or required for energy code compliance, ci R-value must meet IRC Table R702.7(2) and Table R702.7(3), (4), or (5) as applicable based on Climate Zone and the interior VR Class specified. The required minimum ci R-values ensure adequate temperature control to prevent condensation and moisture accumulation within the wall. Increasing ci R-values above code-minimums will further improve thermal performance and moisture control.
Where non-vapor permeable (< 5 perm) ci is used (e.g., FPIS), it will mitigate inward vapor drive from reservoir claddings (e.g., stucco, adhered veneer, brick, etc.). For similar reasons, it is recommended to use a moderate to low perm WRB (e.g., < 20 perm) behind a vapor permeable ci material.
NOTE: Combination of ci and cavity R-value must satisfy energy code, where used or required. They cannot be summed to meet energy code.

Cavity Insulation
If ccSPF is used at thickness to achieve 1.5 perms or less, the R-value can be combined with ci R-value to meet ci requirements of Tables R702.7(3), (4), or (5) to decrease the exterior ci thickness/R-value required, but ccSPF must still be treated as cavity insulation for energy code compliance.*
NOTE: Combination of ci and cavity R-value must satisfy energy code, where used or required. They cannot be summed to meet energy code.
If ccSPF is used at thickness to achieve 1.5 perms or less, the R-value can be combined with ci R-value to meet ci requirements of Tables R702.7(3), (4), or (5) to decrease the exterior ci thickness/R-value required, but ccSPF must still be treated as cavity insulation for energy code compliance.*
NOTE: Combination of ci and cavity R-value must satisfy energy code, where used or required. They cannot be summed to meet energy code.

Anchored Masonry Veneer (stone & brick)
1" ventilation and draining space required for all anchored stone or brick veneer in all climate zones (see Section R703.8).*
Also qualifies as vented cladding for use of Class III VR on walls without exterior ci per Table R702.7(3).
1" ventilation and draining space required for all anchored stone or brick veneer in all climate zones (see Section R703.8).*
Also qualifies as vented cladding for use of Class III VR on walls without exterior ci per Table R702.7(3).

Air Barrier (AB)
A continuous AB is used in all climate zones to achieve required whole buildilng air-change-per-hour (ACH) limits per energy code and to protect wall from moist air intrusion. The designated AB material layer must have joints, seams, gaps, intersections, and penetrations sealed. AB material can be the WRB, the ci, the structural sheathing, the ccSPF cavity insulation, the VR, or gypsum wallboard. Any material or combination thereof must meet energy code requirements for AB material properties (i.e., essentially air impermeable). Recommended best practice is to provide AB on both sides of air-permeable insulation materials (i.e., on exterior and interior sides of wall cavity) for improved thermal performance and moisture control.
A continuous AB is used in all climate zones to achieve required whole buildilng air-change-per-hour (ACH) limits per energy code and to protect wall from moist air intrusion. The designated AB material layer must have joints, seams, gaps, intersections, and penetrations sealed. AB material can be the WRB, the ci, the structural sheathing, the ccSPF cavity insulation, the VR, or gypsum wallboard. Any material or combination thereof must meet energy code requirements for AB material properties (i.e., essentially air impermeable). Recommended best practice is to provide AB on both sides of air-permeable insulation materials (i.e., on exterior and interior sides of wall cavity) for improved thermal performance and moisture control.

Interior Vapor Retarder (VR)1,2
Use of a Class I interior VR (that is not “smart”) in frame walls with a Class I exterior VR is not permitted without an approved design. Double vapor “barriers” should be avoided.
An interior vapor retarder is not required in Climate Zones 1, 2, and 3. Responsive (“smart”) Class I or II VRs are allowed on interior side of any frame wall in all Climate Zones.
If ci used or required: Specify VR per Table R702.7(2) in coordination with ci and cavity insulation R-values per Tables R702.7(3) or (4) as applicable. Class I/II VR must be a responsive (“smart”) VR if ci is FPIS (e.g., non-vapor permeable), otherwise use Class III VR.
If ci not used: Specify VR per Table R702.7(2) with best practice recommendation to specify Class I responsive (“smart”) VR in Climate Zones 5-8 and install as an air barrier. Use of a Class III VR without ci is not recommended even though permitted.
NOTES ON VAPOR RETARDER CLASSES AND RESPONSIVE VAPOR RETARDERS:
Use of a Class I interior VR (that is not “smart”) in frame walls with a Class I exterior VR is not permitted without an approved design. Double vapor “barriers” should be avoided.
An interior vapor retarder is not required in Climate Zones 1, 2, and 3. Responsive (“smart”) Class I or II VRs are allowed on interior side of any frame wall in all Climate Zones.
If ci used or required: Specify VR per Table R702.7(2) in coordination with ci and cavity insulation R-values per Tables R702.7(3) or (4) as applicable. Class I/II VR must be a responsive (“smart”) VR if ci is FPIS (e.g., non-vapor permeable), otherwise use Class III VR.
If ci not used: Specify VR per Table R702.7(2) with best practice recommendation to specify Class I responsive (“smart”) VR in Climate Zones 5-8 and install as an air barrier. Use of a Class III VR without ci is not recommended even though permitted.
NOTES ON VAPOR RETARDER CLASSES AND RESPONSIVE VAPOR RETARDERS:
- Vapor retarder classes are defined in Table R702.2(1) and include Class I (e.g., poly), Class II (e.g., coated kraft paper facer), and Class III (e.g., vapor retarder latex paint per manufacturer’s instructions). Class I has vapor permeance of 0.1 of less, Class II is 0.1 to 1 perms, and Class III is 1 to 10 perms.
- A responsive or “smart” vapor retarder is Class I or II (i.e., 1 perm or less) that becomes more vapor open in a humid environment such that drying occurs when needed. Regular vapor retarders are classified on the basis of “dry cup” vapor permeance measurements at low humidity conditions. Responsive vapor retarders are additionally required to have a permeance of greater than 1 perm when measured by the “wet cup” method of ASTM E96 at a moderately high humidity condition. Coated kraft paper facer is a Class II responsive vapor retarder. Class I responsive vapor retarders are typically proprietary films or membrane products.
For resources to help implement the above graphic for your specific project and climate, refer to: